
VOLUME 11 / NUMBER 1 ISSUE 1 2025
Published for
SUPPLY CHAIN CANADATM
Supply Chain Canada, PO Box 98088, RPO Queen Carlaw Toronto, ON M4M 3L9
Toronto: 416-977-7111 | Toll-free: 1-888-799-0877 | Fax: 416-977-8886 info@supplychaincanada.com | www.supplychaincanada.com
SUPPLY CHAIN CANADA STAFF
President and CEO: Dylan Bartlett
Vice-President of Corporate Services and CFO: Ryan Green
Director of Education and Accreditation: Bess Wong
Corporate Secretary & Manager, Executive Leadership: Jacintha Ward
Information Technology Administrator: Rishu Luthra
Manager, Events and Sponsorships: Janelle Eisler
Manager, Finance and HR: Nikki Hart
Co-ordinator, Marketing and Events: Brooke Metherall
Co-ordinator, Member Experience: Agnes Wong
Supply Chain Canada magazine is published four times per year for Supply Chain Canada.
Published by
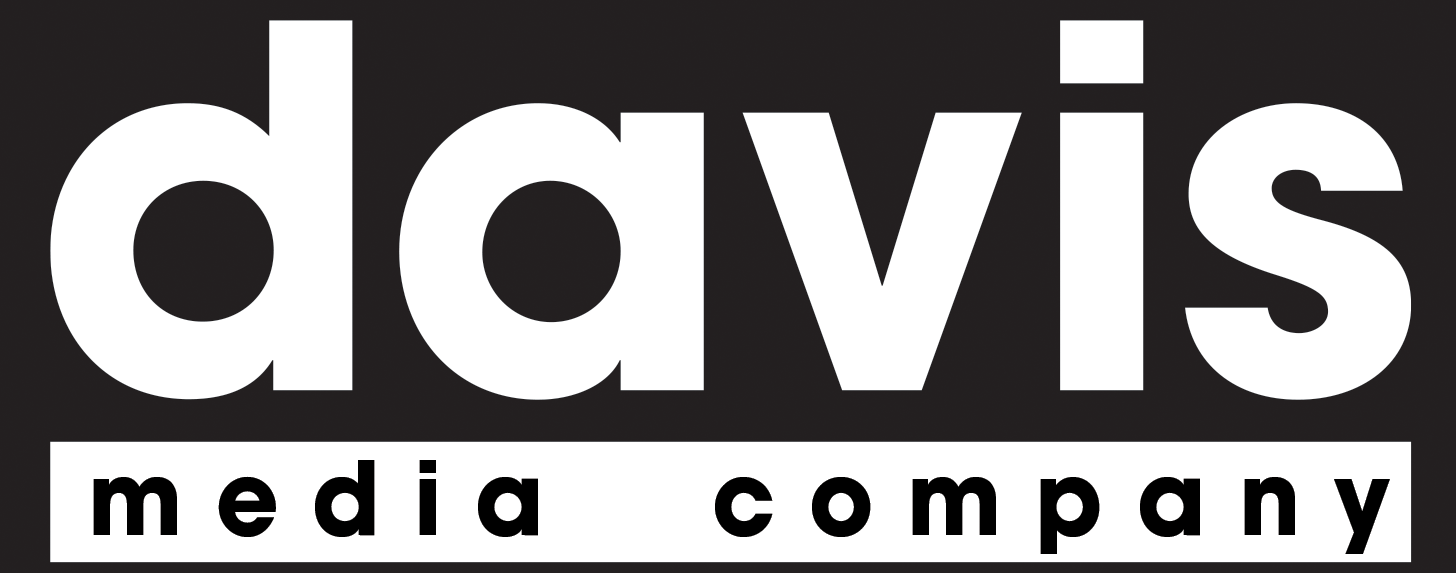
63 Albert St., Ste. 602, Winnipeg, MB R3B 1G4 Phone: 888-705-8870 Email: sean@davismediaco.com | www.davismediaco.com
PRESIDENT
Sean Davis
VICE-PRESIDENT AND PUBLISHER
Jay Cumming
VICE-PRESIDENT OF SALES AND MARKETING
Kara Di Paolo
MANAGING EDITOR
Naomi Lakritz
ACCOUNT EXECUTIVE
Keli Tomlinson
DESIGN & LAYOUT
Sivananthan
© 2025 THE DAVIS MEDIA COMPANY INC. All rights reserved. The contents of this publication may not be reproduced, in whole or in part, without the prior written consent of the publisher. Disclaimer: The opinions expressed by the authors and/or editorial sources contained in Supply Chain Canada are those of the respective parties and do not necessarily represent the opinions of the publisher of Supply Chain Canada.
Cover Photo: © Nourinet / shutterstock.com Publications Mail Agreement # 43361037 Return undeliverable Canadian addresses to The Davis Media Company Inc. Please recycle where facilities exist.
Message from the President and CEO
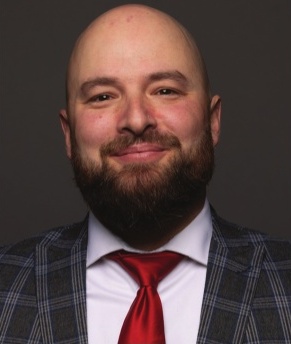
Dylan Bartlett
President and CEO, Supply Chain Canada
NAVIGATING THE SUPPLY CHAIN
EMPOWERING OUR MEMBERS WITH ADVOCACY AND INSIGHTS
T here is a LOT to talk about! Supply chain has been at the forefront of conversations across the country; it’s a pivotal time in our industry. It’s an opportunity to both lead the conversation and create real change. As global trade policies continue to shift, industries across North America are bracing for change. The evolving tariff landscape and ongoing trade negotiations could reshape supply chains, impacting businesses, workers and economies on both sides of the border and beyond.
These reciprocating tariffs will have a significant and concerning economic impact, not only for Americans and Canadians, but also on the global economy. Our hope is that these tactics are part of a larger negotiation strategy, which will lead to more productive conversations, in pursuit of a long-term partnership that involves working more closely together to create economic security and resilience for all parties involved.
At Supply Chain Canada, we are closely monitoring these developments and remain committed to supporting our members through advocacy and insights. We will continue to work diligently to support our members and the supply chain industry.
We’ve also recently partnered with a few organizations to gather feedback and collect data, which we believe will help influence future decisions and help guide us through these challenging times. As part of this process, we will be reaching out to our members directly, working together to share best practices and shape the future of supply chain in Canada.
This is a critical time for our industry and your expertise is needed now more than ever. Supply Chain Canada is looking for industry leaders, innovators and seasoned professionals. If you’re passionate about making a real impact, driving change and guiding the next era of Canada’s supply chain, this is your opportunity. There’s never been a better time to join Supply Chain Canada. Be a part of our network and become a member!
Our 2025 National Conference in Calgary, Alberta from June 11-13 is our biggest conference ever, with tonnes of educational content, exciting speakers and networking opportunities.
And finally, are you following us on social media? We recently celebrated 50,000 followers on LinkedIn, an amazing network of supply chain professionals! Thank you to our many supporters! For all the latest industry news and updates, make sure you follow Supply Chain Canada. Together, we are Professionals Advancing the Future™.
Thank you for your confidence and ongoing support.

Board of Directors
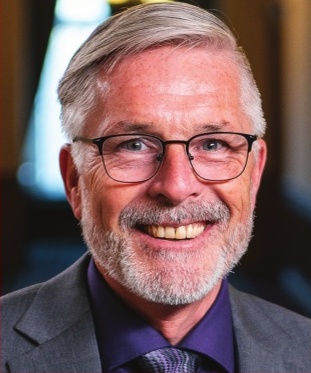
Michael Whelan, SCMP
Board Chair
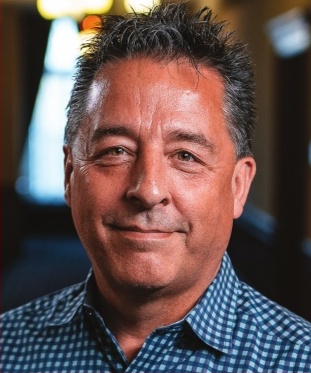
Chris Soroka, SCMP
Board Chair-Elect
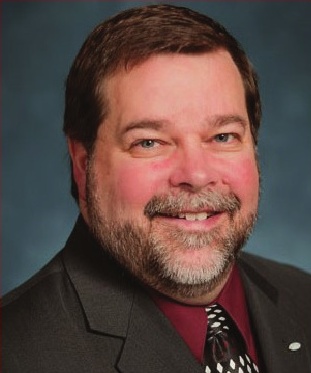
Patrick Gauch
Treasurer
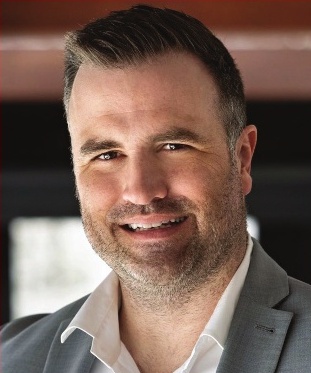
Philippe Blais, SCMP
Director
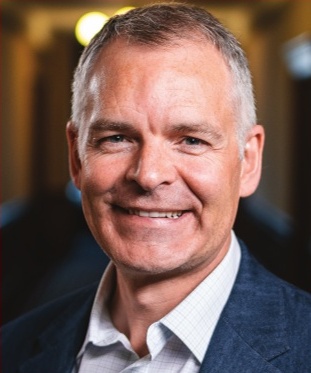
Mike Dalton, SCMP
Director
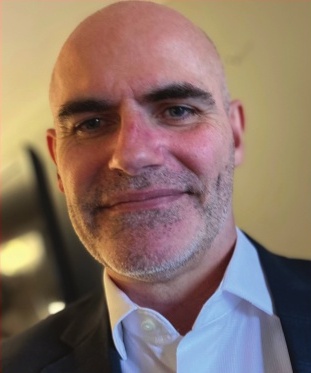
Vincent Dixon, SCMP
Director
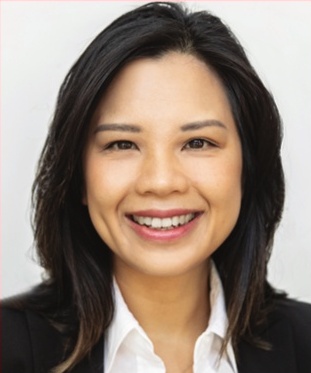
Cindy Kieu
Director
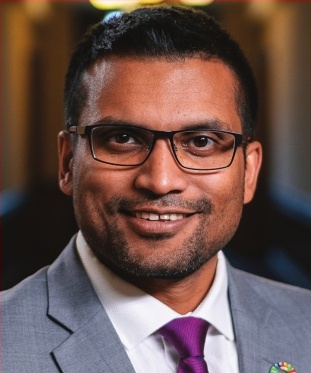
Palash Sanyal
Director
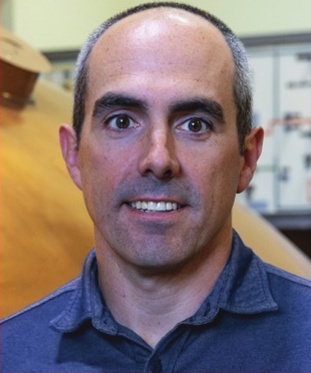
Jack Skerry
Director
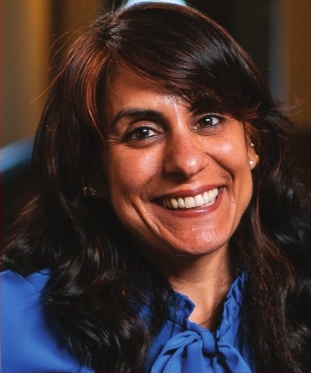
Shalini Talwar, SCMP
Director
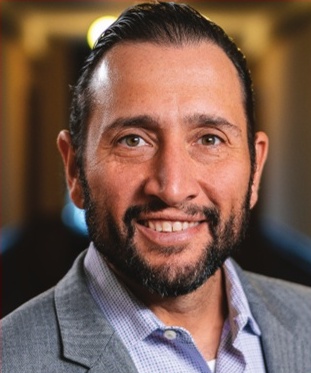
Adam Zanatta
Director
Message du président et chef de la direction

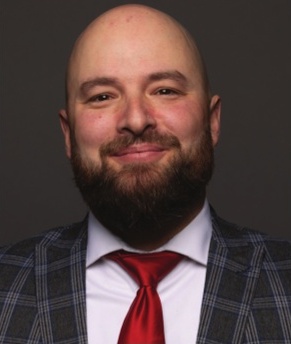
Dylan Bartlett
président et chef de la direction, Chaîne d’approvisionnement Canada
NAVIGUER DANS LA CHAÎNE D’APPROVISIONNEMENT
SOUTENIR NOS MEMBRES PAR DES ACTIVITÉS DE PLAIDOYER ET DE SENSIBILISATION
I l y a BEAUCOUP de choses à dire! La chaîne d’approvisionnement a été au premier plan des conversations à travers le pays. C’est une période charnière dans notre industrie. C’est une occasion à la fois de mener la discussion et de créer un véritable changement. Alors que les politiques commerciales mondiales continuent de changer, les industries de toute l’Amérique du Nord se préparent au changement. L’évolution du paysage tarifaire et les négociations commerciales en cours pourraient transformer les chaînes d’approvisionnement et avoir une incidence sur les entreprises, les travailleurs et les économies de part et d’autre de la frontière et au-delà.
Ces tarifs réciproques auront des répercussions économiques import-antes et préoccupantes, non seulement pour les Américains et les Canadiens, mais aussi pour l’économie mondiale. Nous espérons que ces tactiques font partie d’une stratégie de négociation plus vaste, qui mènera à des discussions plus productives, en vue d’un partenariat à long terme qui implique une collaboration plus étroite pour créer la sécurité économique et la résilience de toutes les parties concernées.
À Chaîne d’approvisionnement Canada, nous suivons de près ces développements et restons déterminés à soutenir nos membres par des activités de plaidoyer et de sensibilisation. Nous continuerons de travailler avec diligence pour soutenir nos membres et l’industrie de la chaîne d’approvisionnement.
Nous nous sommes également récemment associés à quelques organisations pour recueillir des avis et des données qui, selon nous, nous aideront à influencer les décisions futures et à nous guider en ces temps difficiles. Dans le cadre de ce processus, nous communiquerons directement avec nos membres et travaillerons ensemble pour partager les meilleures pratiques et façonner l’avenir de la chaîne d’approvisionnement au Canada.
C’est une période critique pour notre industrie et votre expertise est plus que jamais nécessaire. Chaîne d’approvisionnement Canada est à la recherche de chefs de file de l’industrie, d’innovateurs et de professionnels chevronnés. Si vous êtes passionné par l’idée d’avoir une véritable influence, de conduire le changement et de guider la prochaine phase de la chaîne d’approvisionnement du Canada, vous avez la possibilité de saisir cette occasion. Il n’y a jamais eu de meilleur moment pour se joindre à Chaîne d’approvisionnement Canada. Faites partie de notre réseau et devenez membre!
Notre conférence nationale 2025 se déroule à Calgary, en Alberta, du 11 au 13 juin. C’est notre plus grande conférence à ce jour avec une panoplie de contenus informationnels, d’intervenants passionnants et de possibilités de réseautage.
Et enfin, nous suivez-vous sur les médias sociaux? Nous avons récemment célébré 50 000 abonnés sur LinkedIn, un incroyable réseau de professionnels de la chaîne d’approvisionnement! Merci à nos nombreux supporters! Pour toutes les dernières nouvelles et mises à jour de l’industrie, assurez-vous de suivre Chaîne d’approvisionnement Canada. Ensemble, nous sommes des professionnels bâtisseurs de l’avenirMC.
Merci de votre confiance et de votre soutien continu.

Institutes
National Office
Alberta
British Columbia
Manitoba
New Brunswick
Tel: 506-458-9414
Newfoundland & Labrador
Northern Territories
Toll-free: 1-877-231-0965
Nova Scotia
Tel: 902-425-4029
Ontario
Quebec
Tel: 514-256-0045
Saskatchewan

Institutes
National Office
Tel: 416-977-7111
Toll-free: 1-888-799-0877
Alberta
British Columbia
Manitoba
(for area code 204 only)
New Brunswick
Newfoundland & Labrador
Northern Territories
Nova Scotia
Ontario
Toll-free: 1-877-SCM-N-YOU
Quebec
Saskatchewan
Cover Story
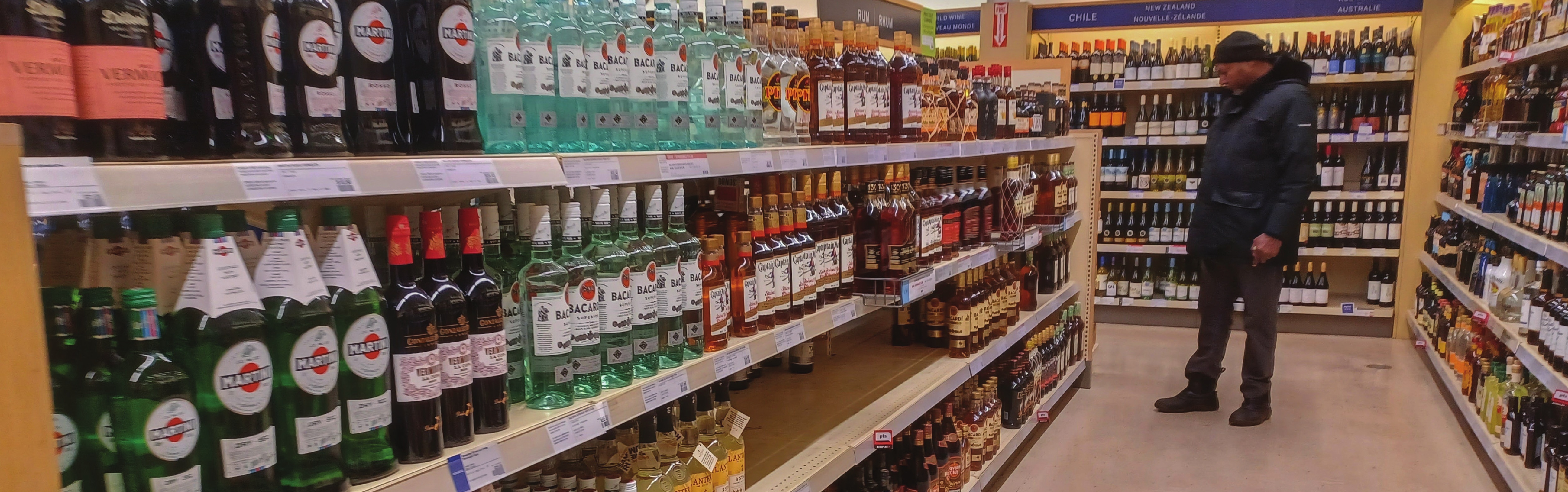
© ACHPF / shutterstock.com
TEAR DOWN THOSE WALLS!
SLOW PROGRESS REMOVING INTERPROVINCIAL BARRIERS STALLS TRADE INTEGRATION
By Mario Toneguzzi
I nternal trade barriers in Canada continue to hinder the country’s economic growth, particularly within the supply chain sector, despite decades of promises to eliminate them.
According to Todd Hirsch, a Calgary economist, author and speaker, provincial interests and political pressures have made it difficult to create meaningful progress in removing these barriers, stalling economic integration across Canada.
Hirsch points out that while the country’s leaders have expressed a desire for a unified internal market, the reality is that entrenched provincial protections and industry-specific demands have thwarted efforts to streamline trade.
The inefficiencies caused by these trade barriers are particularly evident in Canada’s supply chain network, where north-south trade has become far easier than east-west exchanges. This shift has led to missed opportunities for economies of scale, as seen in sectors like brewing, where provinces with smaller populations continue to operate in isolation.
Hirsch argues that without addressing these barriers, Canada is missing out on the kind of efficiency and economic growth seen in other nations that have embraced free trade and specialization.
Despite the challenges, Hirsch believes there is newfound momentum to tackle these barriers, particularly as global trade tensions, such as those with the U.S., have forced Canada to rethink its internal economic strategy. However, the path forward is complicated by informal, ingrained habits that obstruct the flow of goods across provinces. Overcoming these invisible hurdles, alongside dismantling formal rules, will be essential for Canada to unlock its full economic potential and strengthen its supply chain resilience.
“I’m not the only one who’s been saying this, but I do believe that five to 10 years from now, we’ll look back and say, ‘This was exactly the bucket of cold water we needed in Canada.’ We’ve allowed ourselves to become lazy and complacent. Our productivity is low – economists have been sounding the alarm on that for years – and nothing has happened. Now, it has to happen. It’s an existential threat,” says Hirsch. “We really do have the impetus that was lacking in the past, and I think everyone has woken up to the fact that this is ridiculous and we’ve got to get rid of it.”
According to Statistics Canada, approximately $532 billion worth of goods and services were traded across provincial and territorial borders in 2023, accounting for 18.1 per cent of Canada’s gross domestic product (GDP). Of this total, $301 billion (56.6 per cent) was for services, while the remainder was for merchandise trade.
“The contribution of internal trade to Canada’s GDP has seen a notable decline over the last four decades, falling from 26.7 per cent in 1981 to 18.1 per cent in 2023. While internal exports and imports grew by 440.8 per cent during this period, international trade (both exports and imports) expanded at a much faster rate, exceeding 900 per cent growth. This long-term trend highlights a structural shift in Canada’s economy, potentially reflecting factors such as increased international trade agreements, changes in domestic consumption patterns, or shifts in the economic importance of internal trade relative to other economic activities,” said the federal agency.
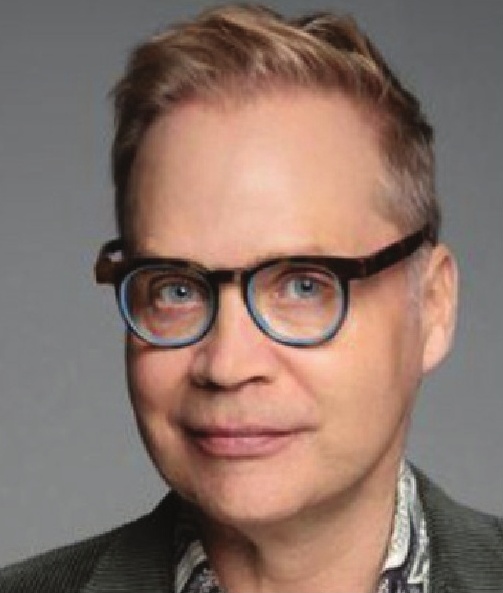
Todd Hirsch Economist
According to a survey by the Canadian Federation of Independent Business (CFIB), nearly 90 per cent of small businesses say removing internal trade barriers should be a priority for governments. Half said internal trade barriers harm production and the same share said they harm expansion, while about 87 per cent agree that food produced in provincially/territorially licensed or inspected facilities should be able to be sold across Canada.
In its 2021 report, “The Case for Liberalizing Interprovincial Trade in Canada,” Deloitte estimated that removing non-geographic trade barriers within Canada could result in an initial 3.8 per cent lift to the country’s real GDP, equalling more than $80 billion.
“It’s been an issue in Canada for pretty much as long as there’s been Canada. These interprovincial trade barriers are the culmination of a series of administrative, technical, regulatory and product movement restrictions that have existed across provinces for a very long time. Our constitution allows provinces to make rules in these areas, and over time, these rules diverge, leading to the trade barriers we see today,” says Michael Holden, chief economist with the Business Council of Alberta.
SeoRhin Yoo, the CFIB’s senior policy analyst, interprovincial affairs, says longstanding interprovincial barriers have been quite a drag on the economy.
“A lot of the interprovincial trade barriers are pretty outdated in modern-day society with our modern supply chain as well as e-commerce. For a lot of small businesses, it prevents them from branching out. It prevents them from expanding, it lowers productivity levels, etc. So it’s very damaging to the economy,” she says.
The Business Council of Alberta’s report, “A Strong Canada. A Good Life,” says Canada is a trading nation but we have a problem when it comes to the movement of goods, services and people between provinces.
“In fact, it can sometimes be easier for companies to trade with other countries than to do business within Canada. Canada relies heavily on international trade to keep our economy going, but with global trade tensions rising, like the U.S. threatening tariffs, it’s more important than ever to fix things here at home and start trading better with each other,” says the report.
The Council says estimates show the following benefits to removing barriers:
• Average wages would rise by 5.5 per cent, or about $1,800 per person;
• Government revenues to fund social programming would increase by 4.4 per cent;
• Corporate profits would rise, attracting more investment to Canada;
• Canadians will enjoy lower prices on goods and services; and
• Many workers will have better access to job opportunities across the country.
Removing the barriers, the Council says, “requires political will, especially from provincial governments. But leaving them up means unnecessarily hamstringing the Canadian economy at a time when we need laser focus on improving it. While internal trade and mobility barriers are largely a provincial matter, the federal government can play a key role in continuing to remove its own exemptions under the Canadian Free Trade Agreement (CAFTA) and creating the environment and incentives to encourage provinces to eliminate barriers to trade and labour mobility.”
The Council’s key recommendations are:
• Incentivize provincial and territorial premiers to reduce interprovincial trade and mobility barriers immediately, starting with meeting the CAFTA eliminations made by former Alberta premier Jason Kenney in 2019, within 90 days. The federal government should tie a portion of federal equalization payments to progress on reducing these barriers;
• Work with provinces and territories to achieve mutual recognition of regulations, rules, standards and policies, enabling the free movement of vehicles, labour, goods and services across Canada; and
• Work with the provinces to simplify interprovincial skilled trades regulations so that immigrants in the skilled trades can work across Canada.
Hirsch says: “We live in a country where we’ve got 10 little fiefdoms and they all want to protect their members. Naturally, there’s nothing evil about this, but they all want to protect their own, and some of these industry associations can be quite powerful politically. So, the premiers tend to bend to what they want.”
Because of the internal barriers, it’s much easier to trade Alberta’s goods with the U.S. rather than with a manufacturer or supply chain provider in Manitoba or Quebec.
“Getting rid of them is going to be harder than we think. There are a lot of what I call ‘phantom barriers.’ These are not rules written down anywhere. If a rule is written down somewhere, it’s easy to identify and get rid of it,” he explains.
“For example, city governments might prefer to procure locally rather than from another province or even out of city. It’s not a law, but it’s a habit or it’s an impulse. These things are harder to weed out, like the beverage manufacturing issues. It’s not a law that says you can’t buy a beverage from another province, but ‘Oh, the label is the wrong size, so we can’t put it on the shelves.’ Crazy things like that.”
“That’s why it’s tough. We can get rid of a lot of the rules, and some provinces are doing a good job, but a lot of it comes down to changing the attitude toward trade across provinces,” Hirsch says.
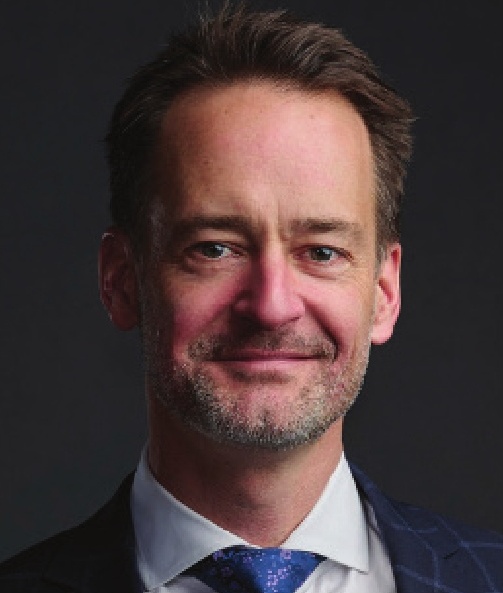
Michael Holden Chief Economist, Business Council of Alberta
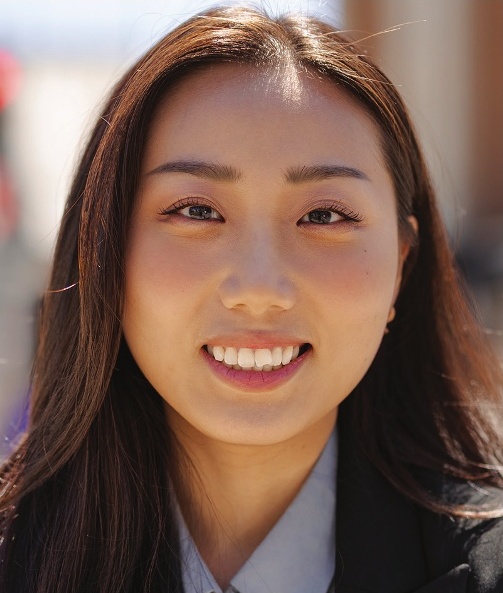
SeoRhin Yoo Senior Policy Analyst, Interprovincial Affairs, CFIB
Holden says the impact of these trade barriers is equivalent to about a seven-per-cent tariff across Canada, which is quite significant.
“There have been various attempts over the years to reduce some of them, but it’s one of those issues that sounds good in theory. But as soon as the rubber hits the road, there’s a reason provinces are unwilling to give some of them up. The momentum we’re seeing around this issue right now is quite remarkable. I will say that the … incremental progress over the last few months has vastly exceeded my expectations,” Holden adds.
“A lot of these barriers involve things like mutual recognition of professional credentials, transportation requirements, trucks allowed at certain times of the day, weight limits and a whole bunch of them related to trucking health and safety and labelling requirements. There are even things like the contents of an emergency kit on a construction site that vary greatly between provinces and disrupt the supply chain.”
Holden adds: “If you’re trying to trade outside your home province, you suddenly have to be aware of a whole series of regulatory, technical and administrative impediments. They’re not really barriers as much as they are a large number of small annoyances that tend to add up. The disruption comes from it being difficult to transport things across the country, with different rules and requirements at every stop along the way.”
Yoo says the internal barriers often prevent a lot of supply chains from moving forward, including goods and services, food, alcohol and labour mobility. Trucking companies must be mindful of a lot of different regulations in the province they’re travelling to, which adds on cost that gets passed down to consumers.
“I think that without the threat of the tariffs, addressing interprovincial trade barriers would have been on the back burner for most Canadian leaders. The tariff threats definitely kind of thrust us into opening talks about internal trade,” Yoo says. “Because we are kind of backed into a corner, we have no choice.”
Logistics Feature
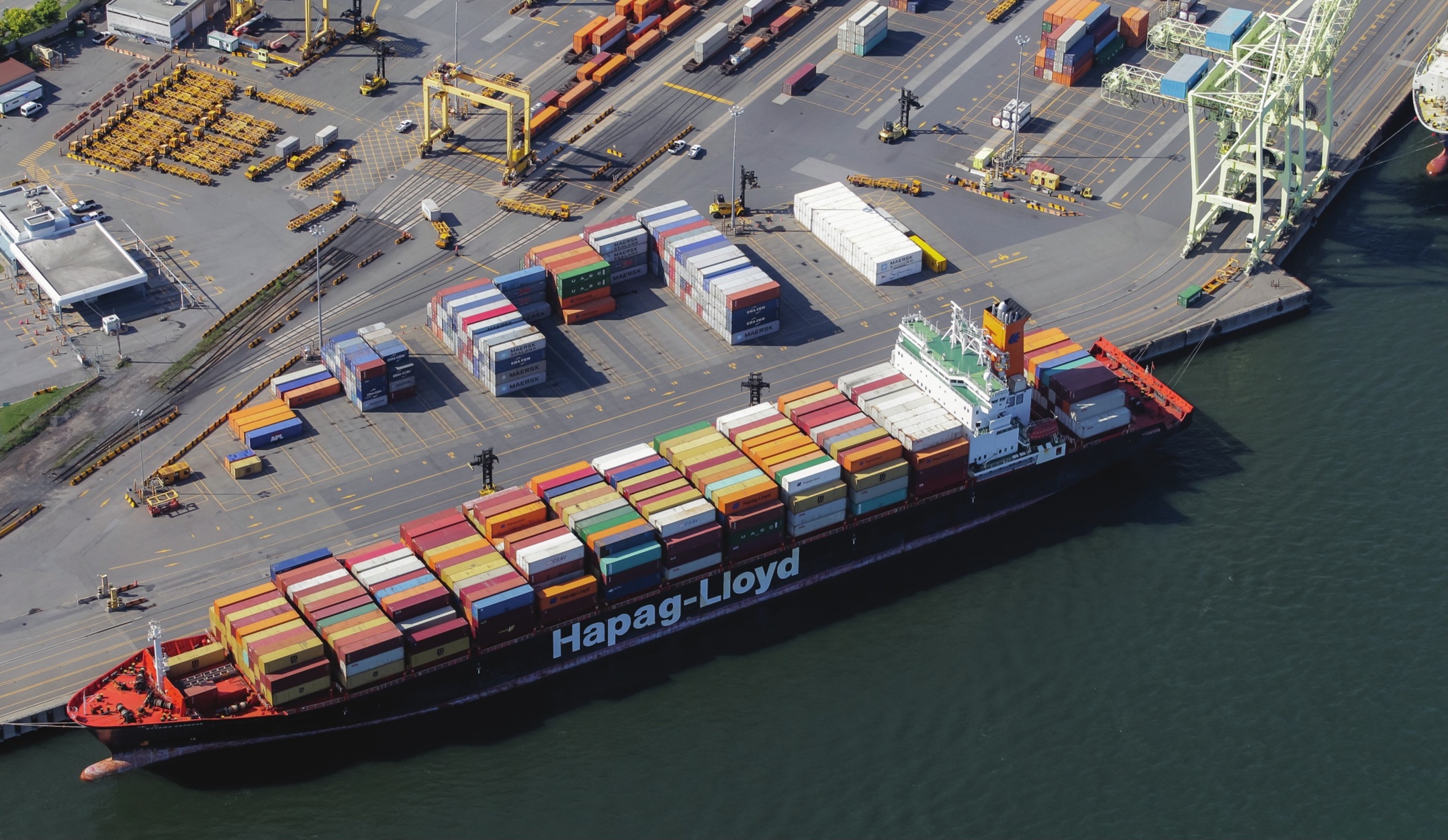
© Patrick Lauzon photographe / shutterstock.com
STORMY SEAS
HOW CANADA’S PORTS WILL WEATHER THE U.S.’S TRADE WAR
By Donald Benham
T he U.S. tariffs and President Donald Trump’s threats to annex Canada are galvanizing the people who run Canada’s ports.
“It’s a wake-up call. Everyone will say that. You hear, ‘Elbows Up!’” says Julie Gascon, president and CEO of the Port of Montreal.
“We are at a very interesting time in Canadian history. I am afraid when I see what is going on, but at the same time, I am confident that as Canadians, we will overcome this. We have to remember our roots. We are a maritime nation. Trading with the world is how this country was built,” she says.
Carly Edmundson, president and CEO of CentrePort Canada in Winnipeg, says Canada should seize the opportunity Trump has presented.
“Now is the time to start having a national conversation. This could be just the right set of circumstances to really get serious about doing something bold with trade and transportation,” Edmundson says.
Greg Rogge, director of land operations at the Vancouver Fraser Port Authority, says the port “is really strongly positioned for Canada and whatever response our government decides to take.”
Canadian ports fare poorly in the 2023 Container Port Performance Index developed by the World Bank and S&P Global Market Intelligence. Montreal ranks 351 and Vancouver ranks 363 out of 405 world ports. The index assesses performance based on the least amount of vessel time in port. Both ports argue that the index’s methodology omits key positive aspects of their operations, but concede Canada’s ports have to up their game. Both ports are also building megaprojects that will greatly increase capacity in future.
Gascon says, “Unfortunately, ports have been a bit overlooked in the supply chain. All our thinking in Canada has been North/South. So now, all of a sudden, we realize we have three oceans bordering our beautiful country.”
The best response to the tariff threat is to increase trade with the more than one billion consumers in countries that are covered by free trade agreements signed by Canada, she says. “If we want to diversify our markets, you’re not going to do that using trucks and trains. You’re going to need ports and you’re going to need ships if you’re going to maintain your economic sovereignty,” Gascon says.
Montreal is adapting to be able to handle more modern container ships, increasing its capacity by 2,000 to 4,000 containers per ship.
Rogge says Vancouver is improving its turnaround times by using modern technology and data sharing to help manage ship, truck and rail traffic more efficiently. The Second Narrows crossing into the port has a rail bridge beneath it that needs to be raised when large ships pass underneath. “This system allows us to optimize when the bridge is up and when it’s down,” he says.
The system also keeps track of trucks coming and going. Terminals must compensate truck drivers for long waiting times, giving them an incentive to reduce turnaround times, Rogge says. Canadian Ports Have a Productivity Problem, an analysis of the World Bank report by MEI – formerly the Montreal Economic Institute – says organized labour must shoulder responsibility for poor productivity.
“Unionized workers often oppose modernization and automation efforts. Protests and labour disputes have taken place at both ends of the country, notably in Montreal, Vancouver and Halifax. Workers in Montreal and Vancouver had to be ordered back to work by the government,” MEI research associate Shal Marriott writes in the analysis.
Marriott called for the federal government to rescind its legislation banning strikebreakers because it “could lead to longer and more frequent strikes at Canadian ports.”
Mark Hancock, national president of the Canadian Union of Public Employees (CUPE) which represents about 1,200 dockworkers at the Port of Montreal, rejected the MEI proposal. “Let’s be 100 per cent clear: We are not going to win the fight against Donald Trump’s aggression against Canada by giving up our hard-won rights,” Hancock says.
“We need to be ramping up protections of Canadian workers and Canadian jobs in the face of this threat, not tearing them down. No amount of gaslighting from the MEI is going to change that.”
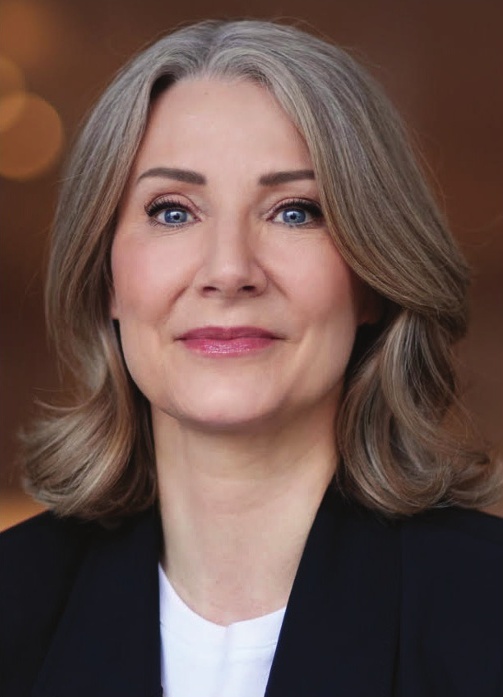
Julie Gascon President & CEO, Port of Montreal
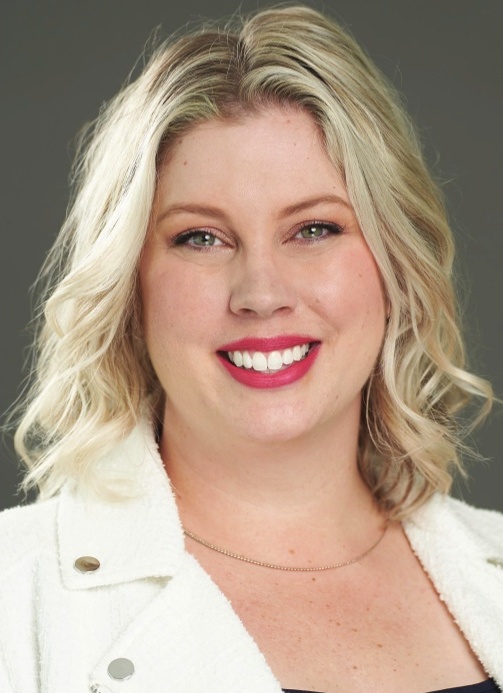
Carly Edmundson President & CEO, CentrePort Canada
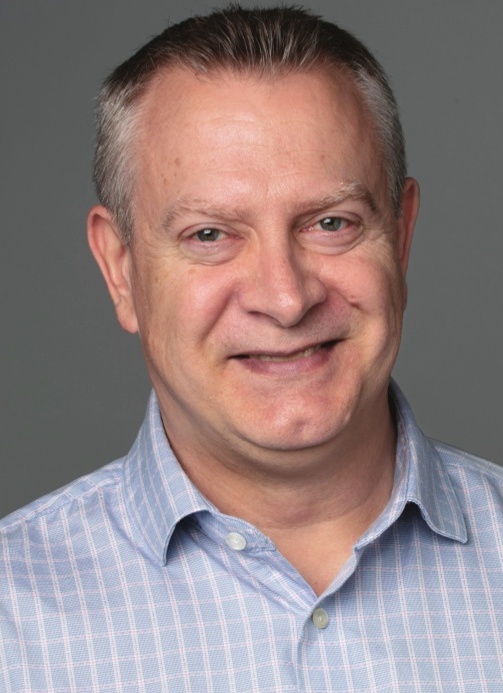
Greg Rogge Director of Land Operations, Vancouver Fraser Port Authority
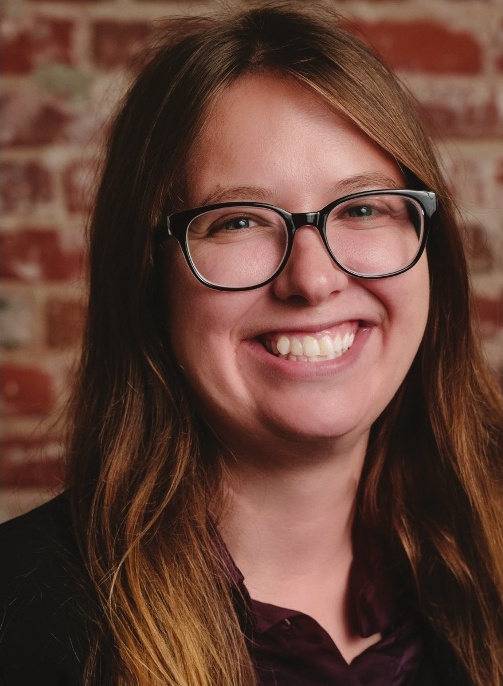
Shal Marriott Research Associate, MEI
Edmundson says CentrePort Canada had to pivot from one of its key selling points after the American threats started. Recalling the pre-Trump era, she says: “We can be used as a gateway to North America. With the strong free trade agreements that were in place and the strong supply chains that we built with our partners to the south of us, it made sense to consider it an almost borderless experience.”
“Now that borderless narrative is certainly not as true as it once was. That’s going to change the way that we’re talking to companies who might want to use CentrePort as their landing point for the continent.”
Instead of heading south, CentrePort is looking north, thanks to a strategic partnership with Arctic Gateway Group, which owns the Port of Churchill and the railway that serves it.
“Any Manitoban needs to understand what having a deep-sea Arctic port could mean, not only for our province, but for Canada. It is on average two days closer to Europe, in comparison to the Panama Canal. Two-thirds of the cost of any product is comprised of the supply chain costs. Two days of time is a massive business advantage,” Edmundson says.
The federal government announced in late March that it was providing funding of $175 million over five years to support operations and maintenance of the Hudson Bay Railway and pre-development activities at the Port of Churchill. Arctic Gateway Group is a partnership of 29 First Nations and 12 isolated communities served by the railway in northern Manitoba. Edmundson says that community ownership is key to making this business model for Churchill different from that of previous owners.
“Their appetite for long-term investment and understanding what the meaning of that port realizing its full potential will be for the people who live in those communities is very different than a company in Toronto that’s looking at it merely as a balance sheet exercise. It changes the timeline. It changes what success means,” she says.
Edmundson remains “very excited about the future of CentrePort and the future of Canada. I know we have some headwinds and some challenges. There will always be those. As long as we continue to think big and are willing to take calculated risk in order to grow, Canada is well-positioned to be a global trade player into the future.”
Inventory Management Feature
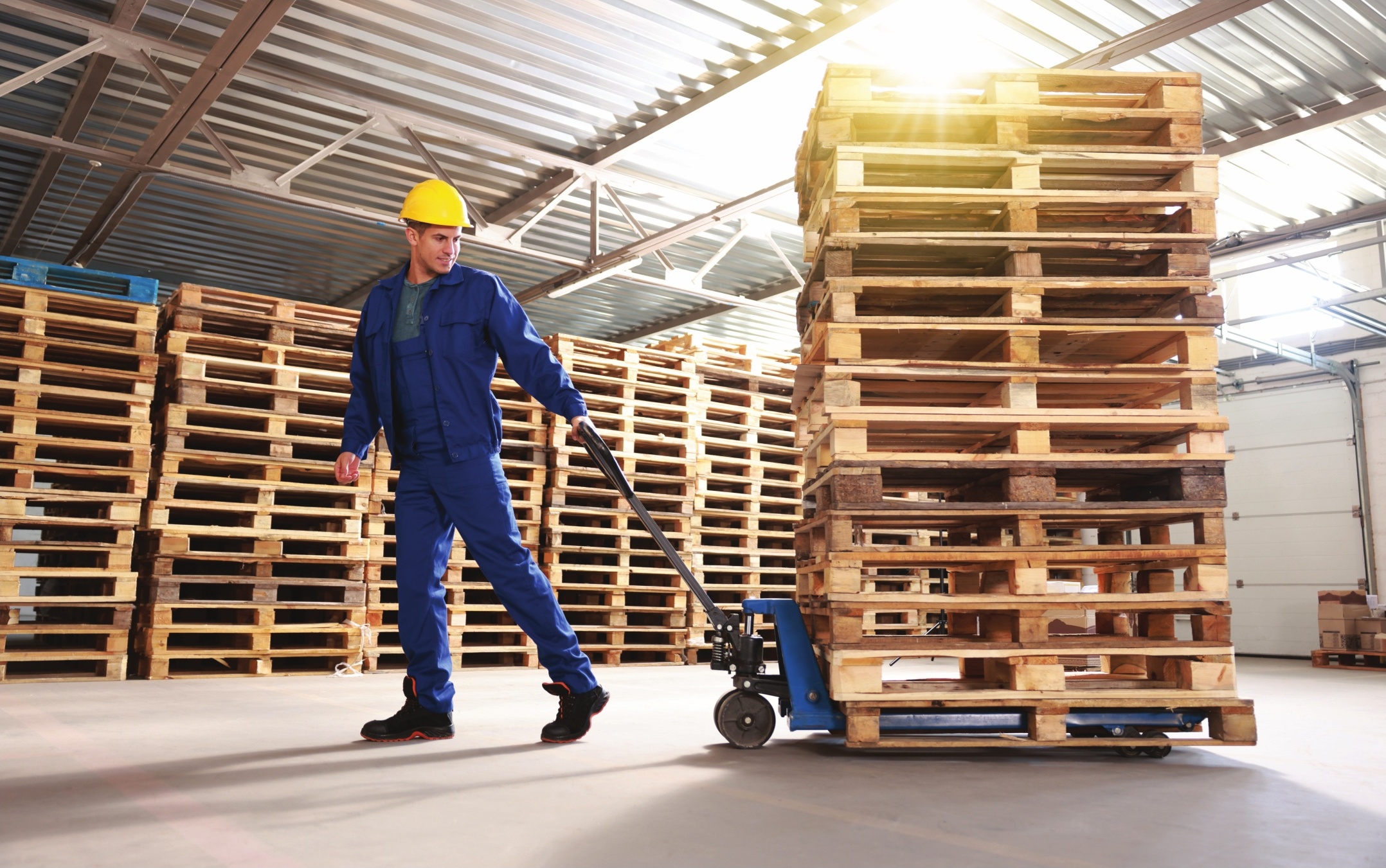
© New Africa / shutterstock.com
GET SAVVY ABOUT SPACE
HERE’S HOW TO OPTIMIZE YOUR WAREHOUSE CAPACITY
By Wendy King
S pace. For your warehouse, it’s the final frontier. And it would be a worthwhile enterprise to scan it carefully and analyze it for improvements.
Since warehouse space is a cost per square foot, optimizing capacity should include examining the footprint, freeing up space for growth and smoothing out the day-to-day flow of goods and labour costs.
One way to decrease the footprint might be to move the warehouse.
“If you move and downsize, would your lease cost savings justify the moving cost?” asks Sean Fiset, senior vice-president at Encor Advisors.
Fiset advises caution, pointing to things like lease negotiations, and adding up the costs of everyday items like stationery and letterhead, the cost of ensuring staff come with you and more. If the warehouse is automated, can the systems be adapted?
A more cost-effective approach might be to stay where you are and optimize your warehouse capacity.
“Warehouse capacity refers to the maximum amount of goods that you can store in a facility while maintaining efficient operation,” says Charles-Antoine Marcil, partner at GCL Group.
A warehouse might suffer from overstock issues and poor configuration of the space. “Maybe they’re taking in too much inventory or maybe the racking is ill-configured for the warehouse,” says Fiset.
“Maybe the racking doesn’t go all the way to the trusses to the underside of the roof, using the full height – the full cube capacity of the building. Other signs it’s being under-utilized would be empty pallet positions or empty storage areas.”
Marcil says additional signs are overcrowded aisles, pallets in the aisles hindering circulation with risks to health and safety and excessive use of temporary storage areas.
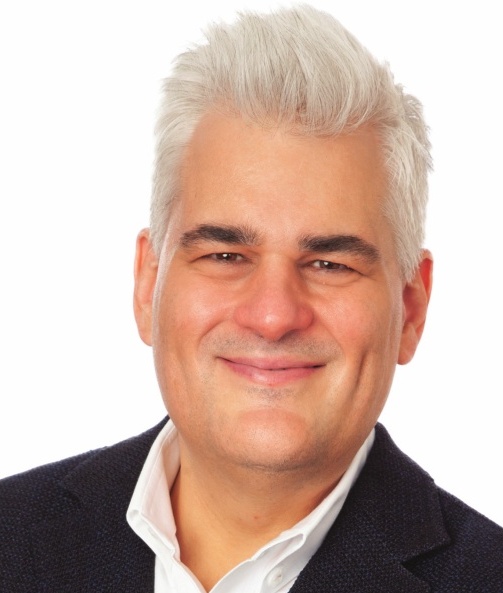
Sean Fiset Senior Vice-President, Encor Advisors
He points to causes such as inefficient warehouse or inventory management, poor layout design, wrong product and improper use of space.
If your warehouse has a problem, it’s time to get hard data and a plan.
“Gather the data to make sure that the decision and opportunities for improvement are based on facts about the way we use our operation,” says Marcil.
“If we’re going to move towards implementing, for example, a warehouse management system, we also need to understand the system architecture that our company uses and the functionality. Maybe we are not using it to the fullest or maybe we need to find a solution that will actually help us to be more efficient in that way.”
Optimizing warehouse space could benefit from consultancy.
“Consultants have this broader perspective – they do these projects many times per month or year – they see different industries, they see best practices and they can bring some new ideas,” says Marcil.
“The ROI for having a team of experts for a couple of weeks or months will greatly benefit the following years in terms of efficiency. We can easily get a 20 per cent reduction in terms of operational cost or we can transpose that to increase productivity by 20 per cent,” he adds.
One benefit of optimization is to reduce “touch” – the number of times a product has to be handled from the time it comes in to the time it ships out.
“You don’t want to bring a product in and then have to move it a bunch of times. It’s got a spot on the shelf. It goes there and then it moves out when it’s been requested,” says Fiset.
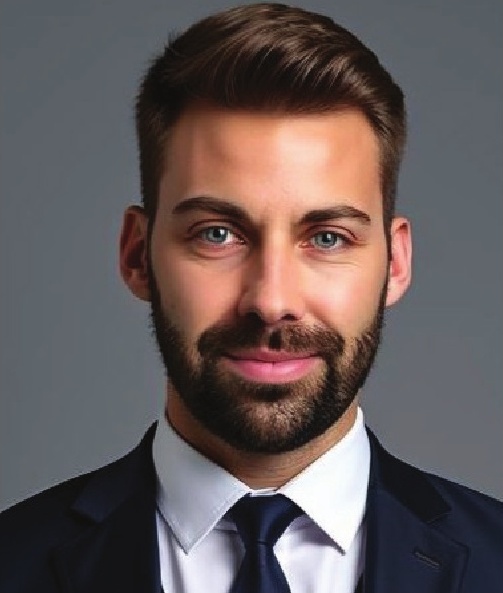
Charles-Antoine Marcil Partner, GCL Group
Fiset says warehouse management software can help with the right layout by showing how quickly items are moving out. Slower moving items could be moved further back and those with high turnover should be readily accessible.
“It’s making sure the pallet positions are being used to capacity, making sure that you know you are fully availing yourselves at the right height,” says Fiset.
“If items are slow moving, you don’t want them in shelves for a long time because you’re paying for square footage you could use for other products. Maybe just decide to cut them from your offering – streamline a bit,” says Fiset.
You need to know exactly what you have to reduce inventory holding cost.
“We’re talking about improving inventory accuracy and also reducing transportation costs, because if you need to transfer product between external warehouses and your main site, if you’re able to streamline, you can reduce those costs,” says Marcil.
It’s important to examine how people work in the warehouse, scheduling, organization and equipment use. Another option to optimize might be adding shifts.
“If you only operate one shift, there’s only so much product that group can get in the door and put on shelves and then subsequently get out,” says Fiset.
He says if one shift isn’t enough time to shelve stock, it could be sitting on the floor creating congestion and inefficiency and needs to be handled again. It can also slow movement of equipment and trucks by creating a bottleneck.
“You may decide, for example, that you need more shipping doors. Then you can lay the product out for each truck in the lane in front of the shipping door, as opposed to staging the product in the aisles, which is going to cause congestion for getting other product,” Fiset says.
“You don’t want to bring a product in and then have to move it a bunch of times.”
Layout and the right equipment are key. Marcil cites examples like:
• Vertical storage, including a mezzanine to allow multi-level picking, automation and advanced inventory management systems;
• Techniques like crossdocking, vendor-managed inventory (VMI) with suppliers keeping some inventory on hand; and
• Different types of racking combined with automation and other technologies to increase the warehouse capacity without expanding the building.
The right equipment is also a matter of product size and flow. Marcil says it is essential that companies get accurate product measurements to determine what type of technology or automation might be best applied.
Fiset points out that automation systems are incredibly efficient but also capital intensive and it may take years to get a return. Automation also lacks something human beings bring to the table – adaptability to change.
“There are warehouses that are completely automated. Canadian Tire has a dark warehouse because it’s just all machines and robotics. But you still need boots on the ground – the system goes down; there’s a power failure that needs to be reset. So many things that could go wrong. There are so many things that are labour dependent,” says Fiset. “Automation works really well, but it’s not highly fluid. It’s not easily changed.”
Automation might bring changes to space requirements for safety of operation, although Marcil says the upside is improved productivity.
“Always consider the humans. The human is part of the warehouse. Train the staff on new technology and processes, bring them to trade shows or conferences,” he says.
“Bring those people in and make them part of optimizing the space because they are doing the work and they need to be part of the solution.”
Warehousing Feature
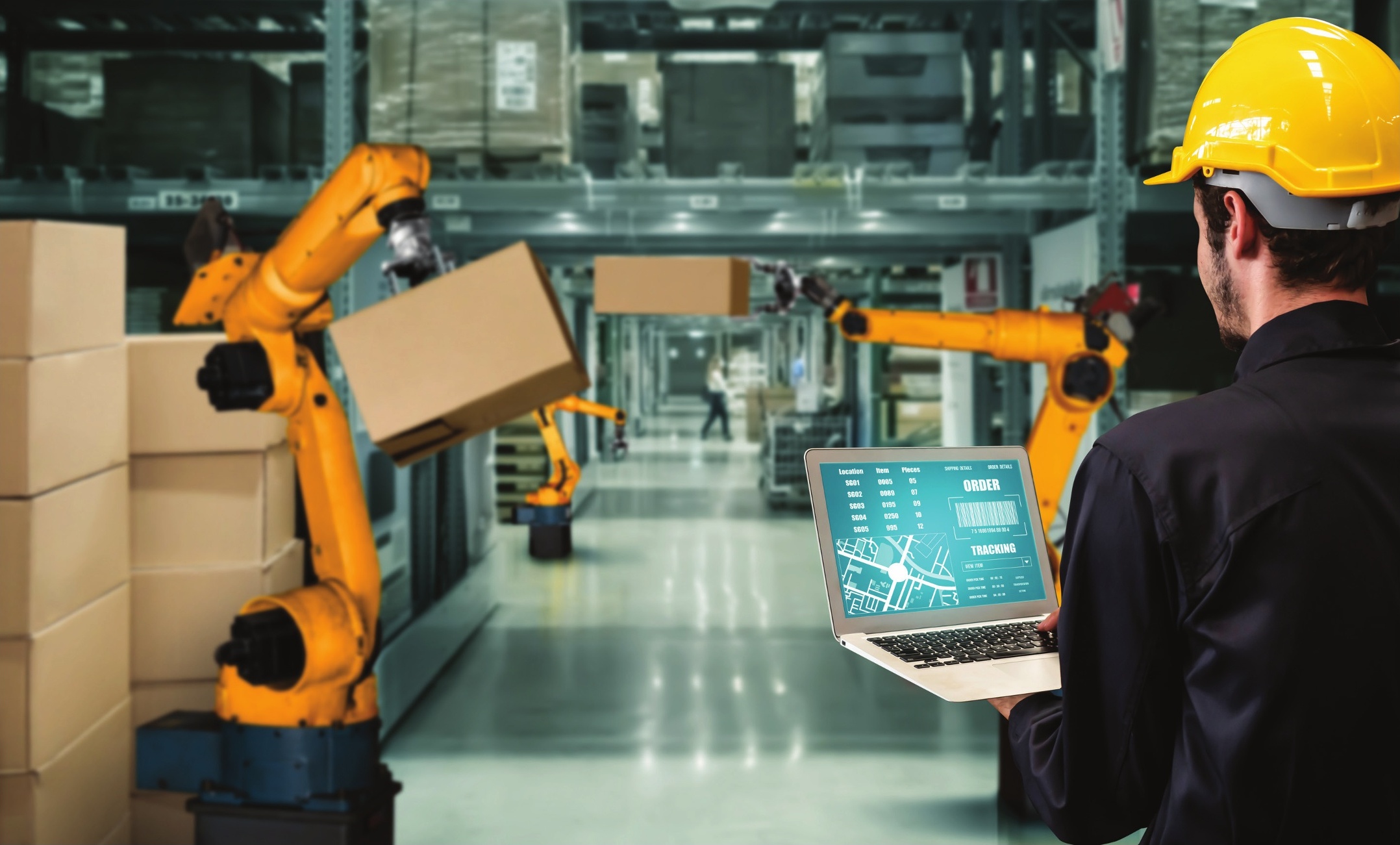
© Summit Art Creations / shutterstock.com
ROBOTS VS. RACKS
THE TRUE COST OF HIGH-TECH WAREHOUSES
By Bryan Hansen
F or decades, warehouses ran on the simplicity of steel racks, fixed aisles and minimal upkeep. Traditional racking systems could last 20 years with little to no maintenance, making them a quiet workhorse of the logistics world. But automation is rewriting that script.
As robots and AI-powered forklifts enter the supply chain, operators are facing a new cost curve. Automated systems demand regular upkeep, software updates and parts replacement, far from the low-maintenance durability of their predecessors.
In her article, “What to Expect in 2025 – 7 Warehousing Trends We Will See,” published in December 2024, Maersk’s digital customer communication manager Silvia La Face writes: “The challenge when implementing automation will remain as cost. The return on investment (ROI) of its implementation requires a payback over a long period.” In some cases, that period can extend five years or more. The message is clear: automation isn’t just a capital expense; it’s an ongoing commitment.
And for distributors and customers alike, that commitment starts with rethinking the warehouse itself.
According to La Face, there are several competing arguments as to whether a brand should continue holding large amounts of stock centrally or shift toward forward-deployed inventory. “With smaller amounts of inventory, that keeps their product closer to the market they are serving,” she writes. “It will be very interesting to see which model is the preferred one.”
2025, she adds, will be the year many companies begin making that choice.
Traditional racking systems, primarily composed of fixed steel, can last more than two decades with minimal maintenance. In contrast, today’s automated guided vehicles (AGVs), robotic picking arms and AI-enhanced inventory tools require continual upkeep. From quarterly tune-ups to software subscriptions and battery replacements, the cost of automation goes far beyond the initial price tag.
Maintenance-related costs, the Maersk article warns, are often underestimated, especially when budgets focus only on capital expenditures. Many warehouse robots rely on lithium-ion batteries that need replacement every three to five years. Software and firmware updates are typically subscription-based and unexpected breakdowns can bring operations to a halt.
Some industry estimates suggest that the annual maintenance cost of a single robot ranges from 10 to 20 per cent of its original purchase price. That kind of recurring cost reshapes the entire budgeting process.
Many logistics consultants warn that automation isn’t plug-and-play. Companies must budget for integration time, staff training and system adjustments.
This shift doesn’t stop at budgeting. As automation reshapes operational costs, it also forces a rethinking of physical space and warehouse design. From floorplans to charging stations, automation changes not just how products move but how entire facilities are built to support them.
The shift to automation isn’t only about machines. It impacts layout, workflow and operations. Traditional racking takes up space vertically. Robotic systems need open floorplans, navigation lanes and charging stations. That means reworking square footage and collaborating with IT and engineering teams.
Warehousing and distribution have always required significant upfront investment but automation adds a new layer of complexity. Operators must now weigh cost against adaptability, with many seeing 24/7 performance, real-time visibility and labour efficiency as essential returns, not just perks. For some, the ability to scale and reconfigure quickly has become a competitive edge.
In 2025, many brands will weigh traditional centralized warehousing models against forward-deployed inventory strategies. Automation plays a central role in both approaches. It’s not just about choosing tech; it’s about aligning warehouse strategy with customer proximity and fulfillment models.
“Robotic systems need open floorplans, navigation lanes and charging stations.”
Maersk’s global head of business development, Simon Oxley, sees visibility and connectivity as top priorities. “For many brands, inventory gets moved from one bucket to another, with knowledge only being available to those working in that specific area,” he says. “2025 will need to demonstrate a better level of connectivity between processes.”
La Face also anticipates continued investment into automation over the next year. “It will be transformative through the whole supply chain,” she writes. That transformation, however, will come with ongoing maintenance and replacement costs.
As maintenance costs rise, the key question becomes: Who absorbs the impact?
Some logistics firms may build these expenses into their base pricing, spreading the cost across long-term contracts. Others are exploring dynamic service fees tied to performance or usage. Either way, warehouse operators will need to communicate these costs clearly whether through maintenance agreements, pricing tiers or co-investment models with clients.
This matters. In an environment where supply chains are expected to be faster, smarter and cheaper all at once, unexpected maintenance bills could strain partner relationships or chip away at margins. Cost transparency won’t just be good practice, it may be essential to sustaining trust.
“These developments might introduce extra costs in terms of maintenance and management, requiring new ways to organize budget allocation and cost control,” La Face writes. In the rush to automate, it’s easy to focus on performance and forget about upkeep. But those hidden costs won’t stay a secret for long. They’ll shape contracts, partnerships and profit margins, raising the ultimate question facing every warehouse operator today.
Warehouse automation isn’t a one-time investment. It’s an ongoing commitment. As robots replace racks, companies must budget not just for performance, but for sustainability. In an industry built on precision and planning, failing to account for long-term upkeep could become the costliest oversight of all.
But for companies willing to plan, invest and adapt, automation still holds promise. The next wave of warehousing isn’t just about moving faster, it’s about building systems that last.
“To be successful in 2025, more businesses will be strengthening their partnerships with integrated logistics providers that can ensure better freedom, flexibility and resilience,” La Face writes.
Three Ways to Budget for Warehouse Automation
-
Don’t skip the maintenance line. Maersk warns that upkeep is often overlooked in projections. Budget for tuneups, software updates and service agreements.
-
Price out long-term battery replacement. Most warehouse robots require new batteries every three to five years. According to industry estimates, replacements can range from $2,000 to $5,000 per unit. These costs can add up quickly.
-
Include system integration and staff training. Automation isn’t plug-and-play. Logistics consultants and supply chain analysts alike emphasize the need to budget for training time and integration across platforms.
Transportation Feature
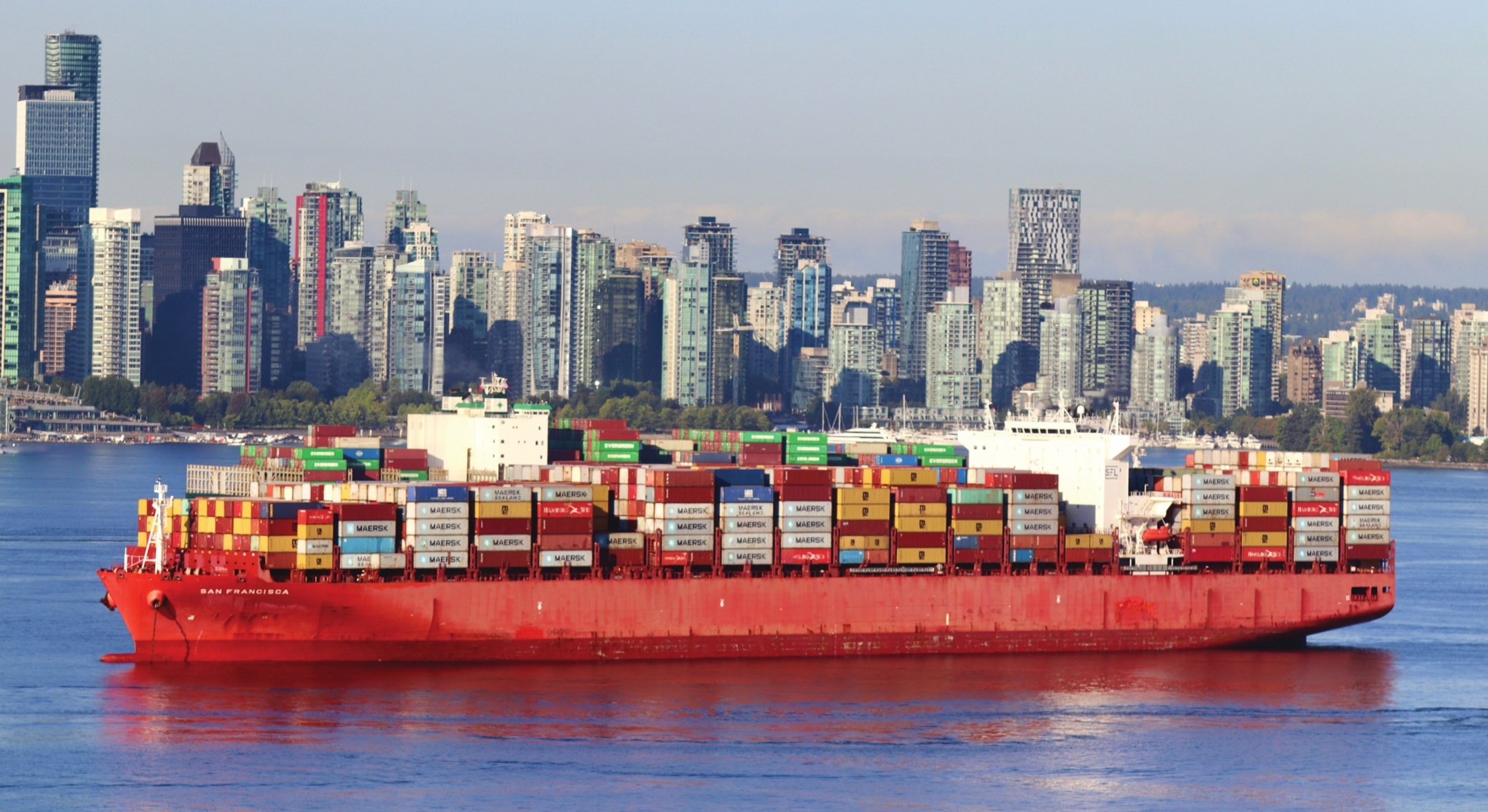
© Macklin Holloway / shutterstock.com
SAILING TOWARD GREENER HORIZONS
LOW-EMISSION, LOW-NOISE PROJECTS UNDERWAY AT CANADIAN PORTS
By Linda Slobodian
A s part of its goal to build a clean transportation system and a green economy, in February Transport Canada announced $35.5 million in funding for three projects in British Columbia to achieve decarbonization of the marine sector along the western coastline.
The investment in commercially available clean technology and infrastructure for ports is provided under the Green Shipping Corridor Program, described by the government as a “key pillar” of Canada’s strategy to transition to low-carbon and net-zero emissions fuels and technologies in the marine sector.
Projects focusing on shore power solutions include increasing the use of clean energy and transportation infrastructure at ports; investing in shore power technology to reduce idling ships’ emissions; and low-emission, low-noise vessels to minimize environmental impact in ports.
Up to $6.6 million was committed to the Vancouver Fraser Port Authority (VFPA) to increase the availability and accessibility of shore power for cruise ships by upgrading infrastructure at the Canada Place Terminal. This project, like all the others, is in the planning stage.
“The Canada Place shore power expansion project aims to enable more visiting cruise ships to plug in while at berth, and we expect expanded shore power infrastructure would result in 30-40 per cent more ships plugging in every season,” says Chance McKee, VFPA’s cruise account representative. “The increasing size and number of cruise ships calling at Canada Place in recent years, combined with our fixed-place connection points, has resulted in some ships berthing out of alignment with shore power infrastructure and unable to plug in.”
The VFPA’s aim is to be “reliable and innovative” in enabling Canadian trade while protecting the environment as part of its commitment to establishing a green cruise corridor on the West Coast. Canada Place was Canada’s first cruise terminal and third in the world to install the technology it is currently working on upgrading.
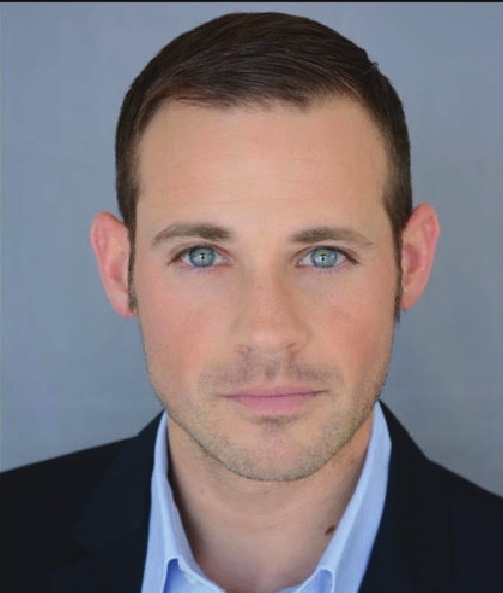
Chance McKee Cruise Account Representative, Vancouver Fraser Port Authority
“Shore power has a crucial role to play, enabling visiting cruise and container ships to shut down their diesel-powered auxiliary engines and plug into B.C.’s low-emission, hydro-powered electrical grid,” said McKee. “The technology has helped reduce port-related greenhouse gas emissions by more than 45,000 tonnes since 2009, the equivalent of taking about 10,700 gasoline-powered cars off the road for a year.”
Another $22.5 million was committed to the Greater Victoria Harbour Authority’s Shore Power Project (GVHA) to help bring renewable shore power to Victoria’s deep-water cruise ship terminal.
This initiative is part of an effort to establish a Green Corridor for cruise travel between Alaska, British Columbia and Washington and part of GVHA’s electrification plan for deep-water port and upland port operations.
“Converting to renewable energy sources will increase the port’s self-sufficiency and strengthen its climate resilience. Shore Power will enable vessels to connect to a clean energy source while berthed, significantly reducing greenhouse gas emissions and improving local air quality,” said GVHA CEO Robert Lewis-Manning.
GVHA has teamed up with BC Hydro and is in the process of accessing costs associated with delivering a power supply to the Breakwater District that is sufficient to provide enough electricity for two large cruise ships and supply the port’s current and future infrastructure needs.
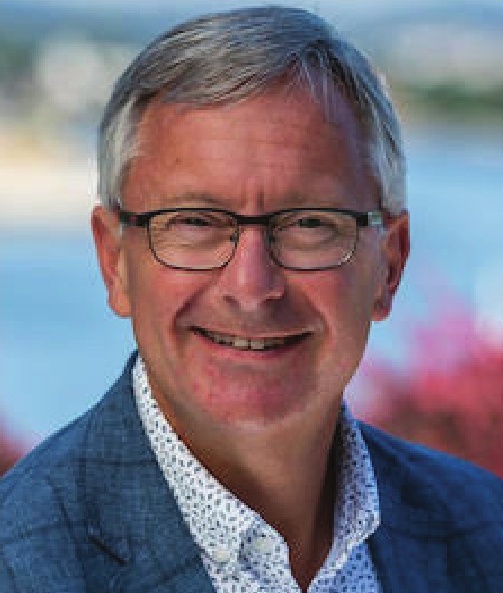
Robert Lewis-Manning CEO, Greater Victoria Harbour Authority
GVHA operates four deep-water berths at the Breakwater District terminal through which 316 cruise ships passed in 2024. It expects 320 cruise ships in 2025. As well, non-cruise ship transporter vessels and a deep-sea cable-laying vessel make their way to the port.
“Shore Power will play a critical role in reducing greenhouse gas emissions across the marine, shipping and cruise industries,” says Lewis-Manning. “Clean energy is important to GVHA. We want to electrify the terminal and our other properties too. We want to go beyond helping cruise ships and provide power to a wide range of vessels and clients.”
GVHA has partnered with First Nations and all levels of government, and is assessing “feasibility, infrastructure needs and funding options.”
“We are also evaluating multiple renewable energy options as the technology landscape is rapidly evolving. It is also critical that we secure further investment from government and industry partners in order to move forward,” said Lewis-Manning.
Transport Canada committed another $6,412,500 to Seaspan Ferries to implement shore power equipment at terminals in Delta, Nanaimo, North Saanich and Surrey and to upgrade four commercial vehicle roll-on/roll-off ferries operating between the terminals.
“Shore Power will enable vessels to connect to a clean energy source while berthed, significantly reducing greenhouse gas emissions.”
The Green Shipping Corridor Program is part of the Canadian government’s plan to protect the environment and meet net-zero emissions by 2050 to which it committed when it signed the United Nations Declaration on Zero-Emission Shipping in April 2022. Funding is provided for projects that help establish green shipping corridors and decarbonization of the marine sector in the Great Lakes, St. Lawrence Seaway and on both coasts.
In July 2024, Transport Canada allocated $1.7 million in grants to 14 projects through the Clean Vessel Demonstration program aimed at spurring the launch of next-generation clean ships and in-shore power technology while prioritizing low-emission, low-noise ships at ports.
Algoma Central Corporation received $597,500 of that total to conduct five studies.
They include: exploring the feasibility of implementing wind-assisted propulsion on Canadian bulk carriers; developing a concept design and carrying out a feasibility study for methanol-fuelled vessels; exploring the technical and economic feasibility and emission reduction benefits of retrofitting Algoma vessels to use shore power; technical work to ensure a wider suite of biofuels can be used that will impact scalability, economic viability and environmental performance of a broader mix of low carbon fuels; and defining the powering of the tug while using the barge as the primary fuel storage. An Algoma spokesperson said it is premature to comment on the projects that are still in the research stage.
Other innovative studies aiming to reduce marine greenhouse gas emissions include $125,000 granted to CSL Group Inc. to develop the technical feasibility and design of the world’s first diesel-electric, battery hybrid laker and her sister ships. Fednav was granted $125,000 for a feasibility study on installing a wind-assisted propulsion system (WAPS) on a bulk carrier and another $125,000 for a feasibility study on installing a battery-based energy storage system on board a Canadian bulk carrier. Mersey Seafoods Ltd. received $125,000 to conduct a feasibility study for using low/zero carbon fuels and technologies for a large offshore fishing vessel.
According to Transport Canada, transportation accounts for 1/4 of all of Canada’s greenhouse gas emissions and marine shipping is responsible for almost three per cent of global emissions.
Naviguer Dans La Chaîne D’Approvisionnement
Soutenir nos membres par des activités de plaidoyer et de sensibilisation
Dylan Bartlett
Tear Down Those Walls!
Slow progress removing interprovincial barriers stalls trade integration
By Mario Toneguzzi
View Desktop Version
Subscribe Now